In many people's cognition, "stainless steel" seems to represent "never rust", but this is not the case. Although stainless steel has a stronger anti-rust ability than ordinary steel, it will still rust under certain conditions. So, under what circumstances will stainless steel rust? What factors will cause stainless steel to rust? I hope you can find the answer after reading this article.
What Is Stainless Steel?
Stainless steel is a large type of alloy steel containing chromium (Cr). Its main feature is that it can form a dense chromium-rich oxide film on the surface of the steel. The film has a self-repairing function and can effectively prevent the oxidation reaction from proceeding, thus having good corrosion resistance. According to its metallographic structure and use, stainless steel can be divided into austenitic, ferritic, martensitic, duplex stainless steel and precipitation hardening stainless steel.
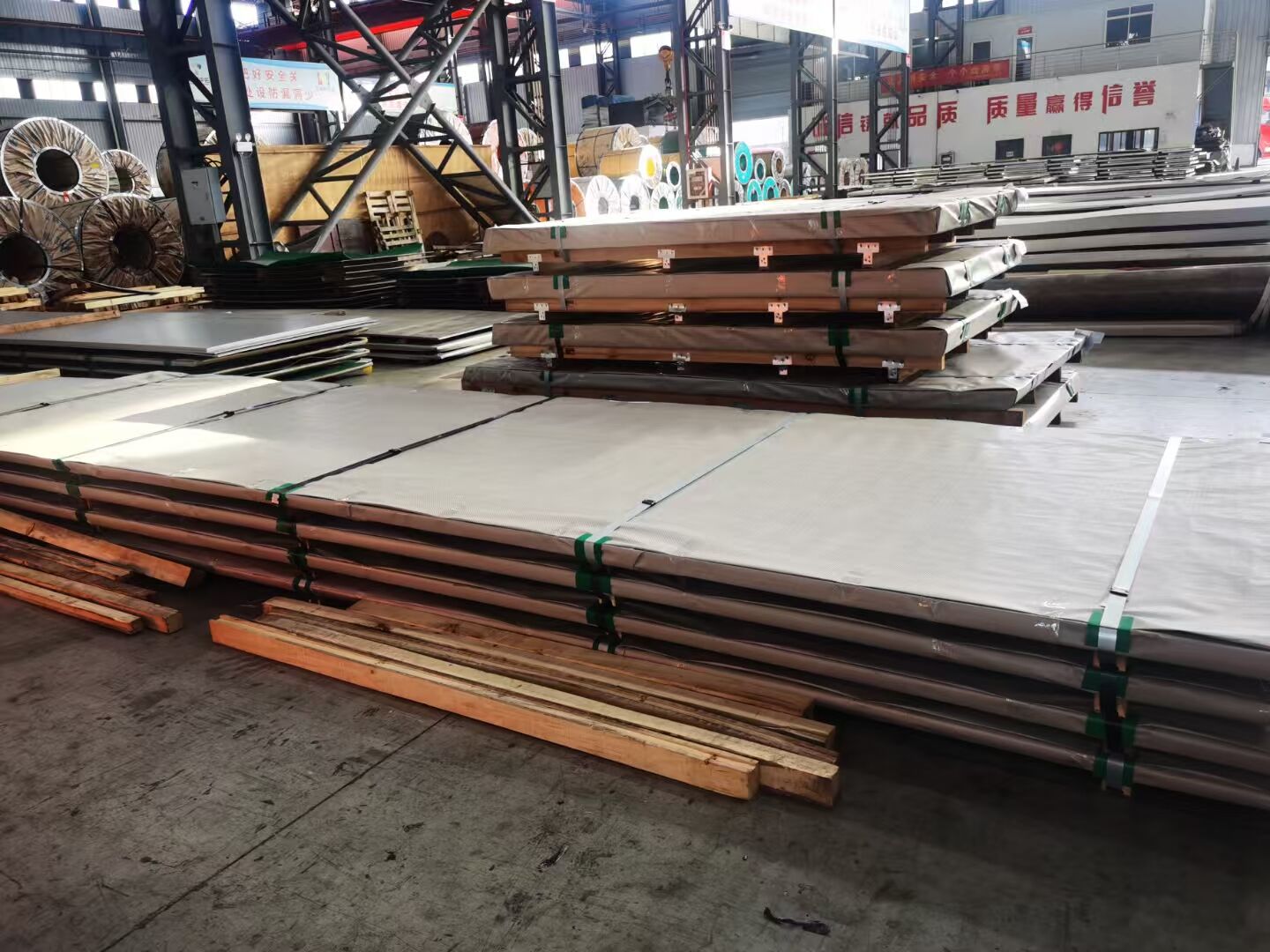
Anti-Rust Ability: Why Stainless Steel Is Better Than Ordinary Steel
The fundamental reason why stainless steel has a better anti-rust ability than ordinary steel is its unique alloy composition and the self-repairing mechanism of the surface passivation film. Ordinary carbon steel is mainly composed of iron. Once exposed to a humid or oxygen-containing environment, it is very easy to oxidize and form reddish-brown rust. Once this rust begins, it will continue to expand and eventually weaken the steel structure. Stainless steel, on the other hand, adds at least 10.5% chromium (Cr) to its alloy. This element has a strong affinity for oxygen and can quickly form a dense, stable, and highly adherent chromium oxide film (also known as a "passivation film") on the surface of the material. Although this passivation film is only a few nanometers thick, it can effectively isolate oxygen in the air and moisture from direct contact with the metal body, thereby preventing further oxidation reactions. More importantly, once this passivation film is damaged in a local area, such as being scratched or contaminated, it can automatically regenerate in the presence of oxygen. This self-healing ability is not possessed by ordinary steel.
In contrast, ordinary steel lacks these alloy protections, and the surface oxide layer is loose and easy to peel off, which cannot effectively prevent the corrosion process. Therefore, stainless steel is significantly better than ordinary steel in anti-rust ability, especially in complex environments such as ocean, chemical industry, high humidity and high temperature, etc., showing more stable and durable performance.
5 Factors Of Stainless Steel Rust And Corrosion
In certain specific environments or conditions, stainless steel will still have rust spots. Usually, when the following factors exist or appear at the same time, the anti-rust performance of stainless steel will decrease, resulting in rust phenomenon:
Chloride Ion
Chloride ion (Cl⁻) is an extremely dangerous corrosive medium for stainless steel. Especially in marine environments, industrial solutions or detergents containing chlorides, chloride ions can destroy the passivation film on the surface of stainless steel, causing local pitting. Once this pitting is formed, the corrosion rate will be extremely fast and extremely difficult to control. For example, stainless steel railings and decorative parts used near the seaside, even if 304 material is selected, will often have rust spots in a short period of time. If 316 or higher grade chlorine-resistant stainless steel is not used, it cannot be guaranteed to be rust-free for a long time.
Acid And Alkaline Media
Although stainless steel can resist most weak acids and weak bases, it is also prone to corrosion in strong acid and alkaline environments, such as high-concentration media such as sulfuric acid, hydrochloric acid, and sodium hydroxide. Most of this type of corrosion is uniform corrosion or pitting.
High Temperature And High Humidity Environment
High temperature increases the rate of chemical reactions. In a humid environment, high temperature accelerates oxidation reactions and reduces the stability of the passivation film, thereby accelerating the corrosion rate of stainless steel. This is particularly evident in some industrial high-temperature equipment.
Heat-Affected Zone Corrosion In The Welding Area
High temperatures generated during welding may cause coarse grains and carbide precipitation in stainless steel welds and heat-affected zones, thereby forming a "chromium-poor zone" and causing the weld area to lose its passivation ability. This phenomenon is called "intergranular corrosion". If the appropriate welding process is not adopted or subsequent solid solution treatment is not performed, rust is very likely to occur near the weld, affecting the overall structural strength.
Surface Scratches Or Impurity Adhesion
The corrosion resistance of stainless steel depends on the integrity of the surface passivation film. If the surface is scratched or hit during transportation, installation or use, causing the passivation film to rupture, the water vapor and oxygen in the air can directly contact the metal matrix, thus causing rust. At the same time, if some impurities such as iron filings, dust, sand particles, etc. left over during the construction process are not removed in time, they will also cause "electrochemical corrosion" under the action of moisture, inducing rust spots.
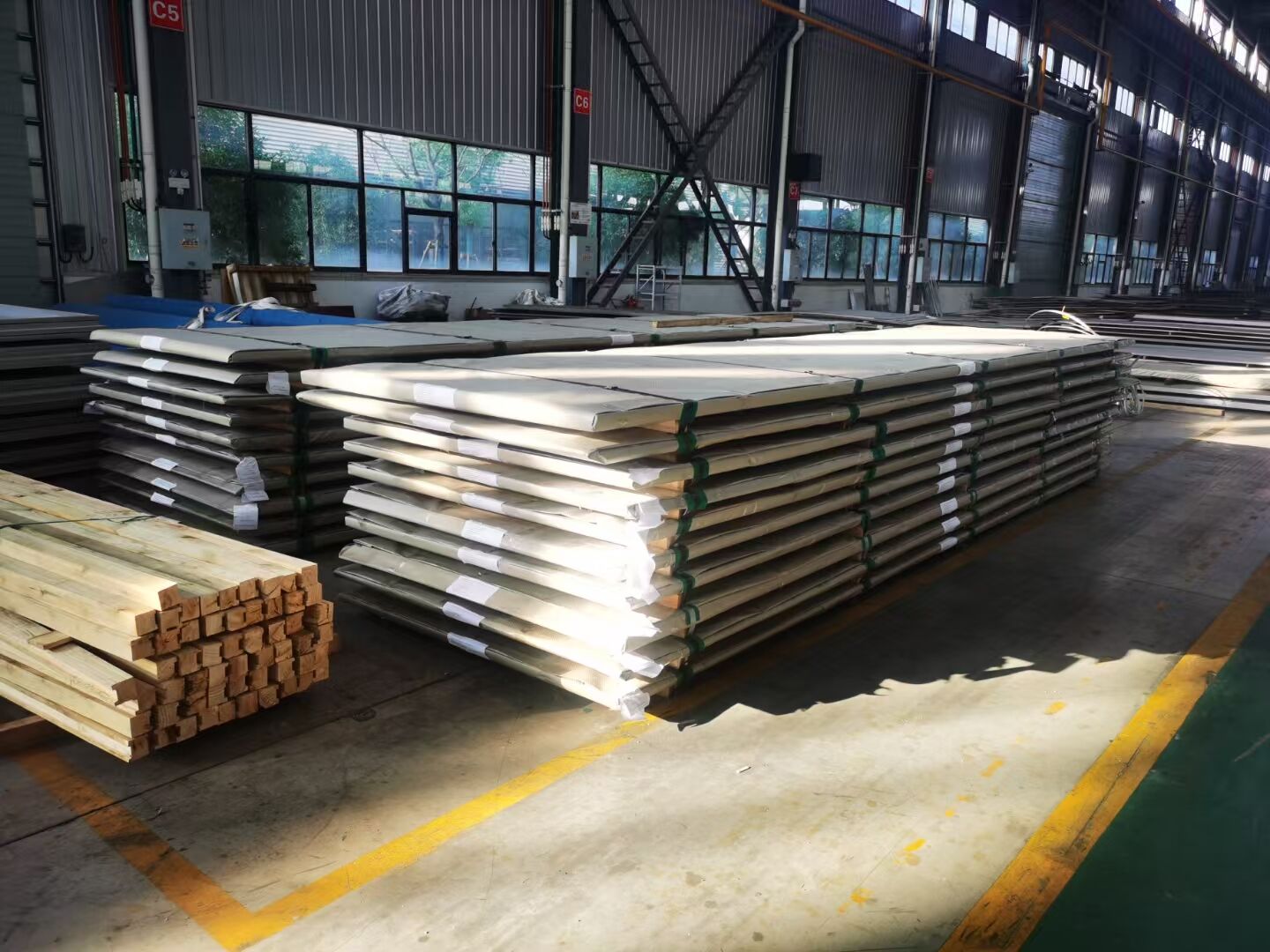
What Are The Types Of Stainless Steel Corrosion?
Uniform Corrosion: This is the most common type of corrosion. The metal surface is uniformly attacked, the overall luster is lost and the thickness is thinned.
Pitting: Pitting is a form of local corrosion. The surface looks intact, but it is actually perforated. It often occurs in chlorine-containing environments.
Crevice Corrosion: It occurs in the gap or joint area, which is common in bolted connections, flanges, welds, etc. Due to poor ventilation inside the gap, the local solution is acidified, causing corrosion.
Stress Corrosion Cracking: Cracks are generated under the combined action of specific corrosive media and tensile stress, which eventually leads to material rupture. Commonly seen in heat exchangers, pressure vessels, etc.
Intergranular Corrosion: Corrosion between grains, especially during welding or heat treatment, is common in austenitic stainless steel after heating in the sensitization temperature range.
Electrochemical Corrosion: When stainless steel comes into contact with other metals and electrolytes are present, a primary cell is formed, leading to corrosion.
How To Prevent Stainless Steel From Rusting And Corroding
-
Choose the right material: Choose the right type of stainless steel according to the use environment. For example, it is recommended to use 316 or higher grade alloy steel in the marine environment, and avoid using 304 in a high chlorine environment.
- Surface treatment: Use sandblasting, pickling passivation, polishing, electrolytic polishing and other methods to remove surface impurities and enhance the stability of the passivation film.
- Reasonable design of structure: Try to avoid dead corners and gaps to facilitate cleaning and ventilation, and reduce the occurrence of crevice corrosion.
- Regular cleaning and maintenance: Regularly clean surface pollutants with clean water or special cleaning agents to avoid the adhesion of metal particles, oil stains, salt, etc.
- Control the use environment: control the pH value, chlorine content, temperature and humidity of the use environment as much as possible, and maintain good ventilation.
FAQ:
1. Why does 304 stainless steel also rust?
Although 304 stainless steel has good corrosion resistance, its passivation film is easily destroyed in an environment with high chloride ion concentration (such as the seaside, places where bleach is used, etc.), which leads to pitting or crevice corrosion.
2. Yellow or brown spots appear on the surface of stainless steel. Is it rusted?
Usually this is rust caused by surface pollutants, such as iron oxide powder, processing residues, etc. You can use a stainless steel cleaning agent to remove it and observe whether there are any signs of corrosion.
3. Why is stainless steel prone to rust after welding?
The welding process will change the metallographic structure of the material. If the subsequent pickling and passivation or treatment of the weld area is not performed, intergranular corrosion or stress corrosion is very likely to occur.
4. Can stainless steel be exposed to the seaside or swimming pool for a long time?
Yes, but you need to use high-alloy stainless steel such as 316, 2205 or super stainless steel, and strengthen daily maintenance and design anti-corrosion measures.
5. How to judge whether stainless steel has corroded?
Rust visible to the naked eye, surface discoloration, roughness or through surface potential test, stainless steel corrosion rate test can determine whether corrosion has begun.
HNJBL is a professional steel manufacturer and supplier. Our company's main products include carbon steel, stainless steel, wear-resistant steel, steel profiles, coated steel, etc. Complete specifications, stable quality, and sufficient quantity.
+86 17611015797 (WhatsApp )
info@steelgroups.com