Stainless steel has become the material of choice in several industries due to its superior corrosion resistance, durability and aesthetics. Among the many grades of stainless steel, 304 and 316 stainless steel are the two most commonly used. So how to choose between 304 stainless steel and 316 stainless steel? Let’s take a look together!
What Is Stainless Steel?
Stainless steel is a family of iron-based alloys containing at least 10.5% chromium. The addition of chromium forms a thin, invisible chromium oxide film on the steel surface, protecting it from corrosion. This passivation film has the ability to self-repair. Even if it is damaged, it will repair itself in the presence of oxygen.
What Are The Classifications Of Stainless Steel?
Stainless steel can often be divided into several categories according to its organizational state, including austenitic, ferritic, martensitic and duplex stainless steel. Among them, 304 and 316 stainless steel are austenitic stainless steel and are the two most widely used grades.
Characteristics Of Austenitic Stainless Steel:
Austenitic stainless steel has a face-centered cubic crystal structure, is non-magnetic at room temperature, and has excellent toughness and ductility. They can be cold worked to significantly increase their strength while maintaining high toughness and corrosion resistance. This type of stainless steel exhibits excellent corrosion resistance in most environments due to its high content of nickel and chromium.
Definition of 304 stainless steel and 316 stainless steel:
304 stainless steel:
304 stainless steel is the most commonly used austenitic stainless steel. Its composition includes 18-20% chromium and 8-10.5% nickel, with smaller amounts of carbon, manganese, silicon and nitrogen. The high content of chromium gives it good corrosion resistance in oxidizing acid environments, while nickel enhances its toughness and ductility.
316 stainless steel:
The composition of 316 stainless steel is similar to 304 stainless steel, but also slightly different. The main difference is the addition of molybdenum. The addition of molybdenum significantly improves its corrosion resistance, especially in chloride-containing and acidic environments.
304 VS 316
Chemical composition:
Grade
|
C
|
Mn
|
Si
|
P
|
S
|
Cr
|
Mo
|
Ni
|
N
|
304
|
≤0.08
|
≤2.0
|
≤0.75
|
≤0.045
|
≤0.030
|
18.0-20.0
|
-
|
8.0-10.5
|
≤0.10
|
316
|
≤0.08
|
≤2.0
|
≤0.75
|
≤0.045
|
≤0.030
|
16.0-18.0
|
2.0-3.0
|
10.0-14.0
|
≤0.10
|
Mechanical properties:
Grade
|
Tensile Strength (MPa)
|
Yield Strength 0.2% Proof (MPa)
|
Elongation (% in 50mm)
|
Hardness
|
Rockwell B (HR B)
|
Brinell (HB)
|
304
|
515
|
205
|
40
|
92
|
201
|
316
|
515
|
205
|
40
|
95
|
217
|
Corrosion resistance:
304 stainless steel has good corrosion resistance in most environments, but is prone to pitting in high chloride or acidic environments. In contrast, 316 stainless steel contains molybdenum, which can better resist pitting and crevice corrosion caused by chlorides. Therefore, in marine environments or chemical industries, 316 stainless steel is usually a better choice.
Application:
304 stainless steel is mainly used in these fields: food processing equipment, household appliances, kitchen utensils, construction applications, chemical containers, etc.
316 stainless steel is mainly used in these fields: marine environment, chemical processing, medical equipment, pharmaceutical equipment, etc.
Cost considerations:
Although 316 stainless steel is slightly better in performance, it is relatively high in cost. This is mainly because the molybdenum element contained in 316 stainless steel is relatively rare, which leads to an increase in its production cost. Therefore, in cost-sensitive fields such as household goods, architectural decoration, etc., 304 stainless steel is often more popular. In professional fields with extremely high requirements for corrosion resistance, such as marine engineering and chemical industry, 316 stainless steel can win a place with its excellent performance.
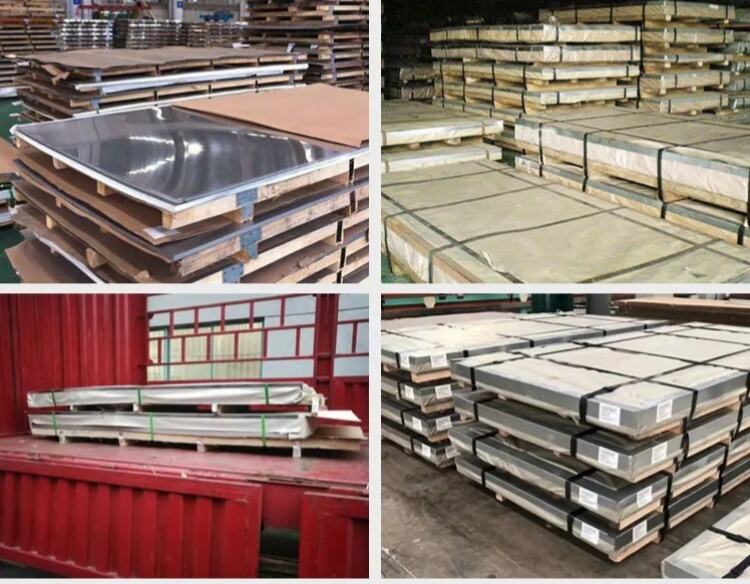
In practical applications, choosing the right type of stainless steel can not only ensure the long life and good performance of the material, but also optimize cost-effectiveness. Therefore, in the material selection process, the specific needs and environmental conditions of the application must be carefully analyzed to make the most appropriate decision.